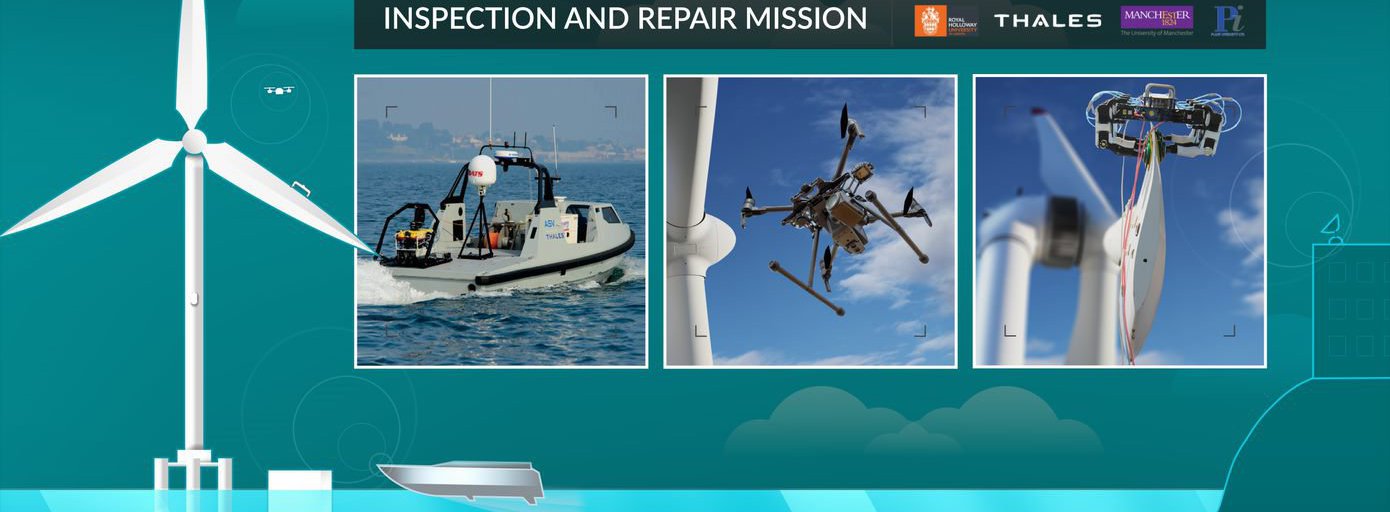
MIMRee will demonstrate how autonomous robotic systems are capable of operating offshore wind turbine blade inspection and repair missions remotely.
At a glance
The MIMRee will
- Remove the need to send humans offshore to carry out wind turbine blade IMR tasks;
- Remove the need to shut wind turbines down to carry out blade inspections;
- Reduce the risk of using autonomous vehicles offshore to carry out asset IMR tasks;
- Safely demonstrate a fully autonomous approach to blade IMR tasks in real-world operating conditions;
- Establish the business case for using autonomous vehicles for blade IMR;
- Develop a roadmap for transferring the MIMRee system to other relevant industries.
Key details
Gallery
More information
The challenge
The inspection and repair of offshore wind turbines are currently performed by rope access technicians. The challenging offshore conditions bring a multitude of risks including lightning strikes, squalls and gales, as well as wave heights that can make transfer from vessel to the wind turbine platforms highly dangerous.
The MIMRee system will introduce a step-change in the Operations and Maintenance (O&M) of offshore wind farms by removing humans from the loop during the inspection, maintenance and repair (IMR) of offshore wind turbine blades. The aim is to significantly reduce the costs and turbine downtime associated with these tasks and reduce the H&S risks of using rope access technicians.
Our approach
The developed MIMRee system will comprise of an Autonomous Surface Vessel (ASV) with capabilities to autonomously transport, charge and deploy UAVs and blade IMR robots at offshore wind farms. The UAVs will be developed to both autonomously inspect wind turbine blades and deploy blade IMR robots on stationary wind turbine blades. The blade IMR robot will be developed to conduct both autonomous NDT inspections and maintenance and repairs of wind turbine blades.
RCA’s Autonomous Repair Arm in Action. As of June 2020, fully integrated with Robot Operating System is an Autonomous Repair Arm for resurfacing blades developed by RCA Robotics Laboratory. The arm can rapidly switch between modules for cleaning, sanding and topcoating damaged areas of blades, providing real-time feedback visualisation and human-in-the-loop teleoperation of repair tasks via a bespoke user interface system.
Visit reNEWS.biz for a more complete review of project milestones that has been achieved during its first year.
Outputs
Bernardini, S., Jovan, F., Jiang, Z., Watson, S., Weightman, A., Moradi, P., Richardson, T., Sadeghian, R., Sareh, S. (2020) A Multi-Robot Platform for the Autonomous Operation and Maintenance of Offshore Wind Farms. Proc. of the 19th International Conference on Autonomous Agents and Multi-Agent Systems (AAMAS-20).
Ask a question
Get in touch to find out more about our research projects.
[email protected]
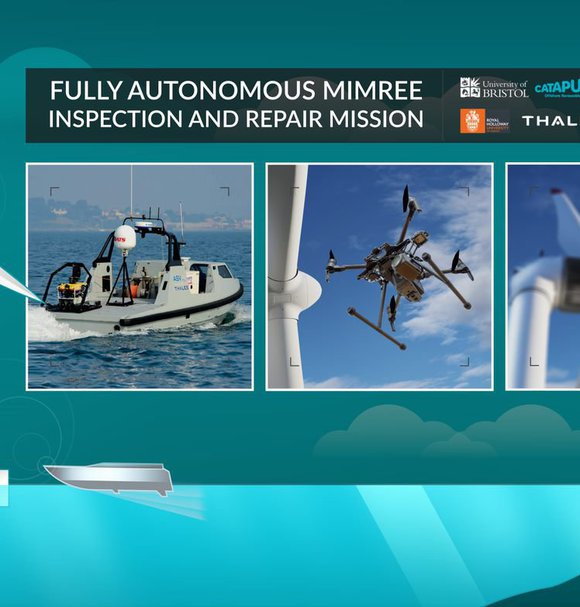